
Description
Metalwork (kinkō) is the art of crafting objects from metal. Metal is an important material used to produce a wide variety of objects used in everyday life. The properties of metal vary significantly from the materials of other craft categories.
Process
- STEP 1A metal is selected
- STEP 2
- The form is cast
- The form is hammer formed
Metal casting (chūkin) is the process of creating forms by pouring molten metal into a mold and then allowing the metal to cool and harden. Forms may be created using different techniques, such as lost-wax casting (rōgata), clay mold casting (sōgata), or sectioned mold casting (komegata). The mold is essential to the casting process.
Hammer forming (tankin) is the process of expanding and shaping metal by striking it with a hammer. The metal is repeatedly heated to increase its malleability and worked with a hammer while soft.
- STEP 3Ornamentation is applied
Chisels and punches with specially shaped heads are used to embellish the piece or produce recesses for metal inlay or other decorations.
Artistic Techniques
Casting
Forms are cast from molten metal
Lost-wax casting
In lost-wax casting (rōgata), a wax model is coated with a refractory of sand and clay to produce a mold. The mold is then heated until the wax melts out of it. Next, molten metal is poured into the mold. Once the metal has cooled, the mold is broken open. By melting away the wax, a work of metal may be produced in the exact form of the original wax model.
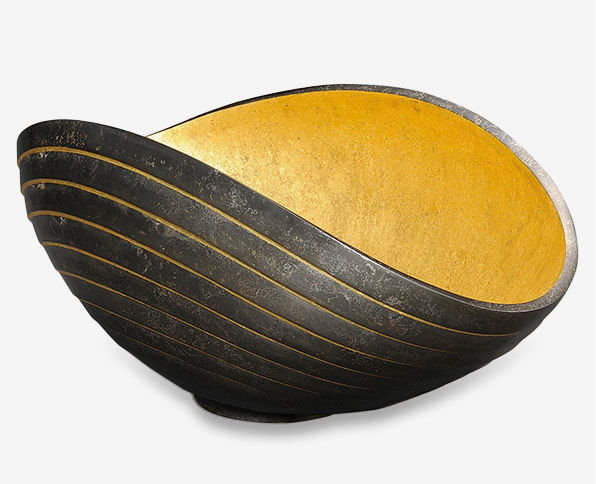
Clay mold casting
In clay mold casting (sōgata), a symmetrical mold is produced by rotating a template called a strickle board in a mixture of sand and clay to shape the walls of the mold. Clay mold casting is predominantly used to produce tea ceremony kettles and temple bells. After the piece is removed from the mold, it is heated and painted with lacquer (urushi) or a solution of iron, vinegar, and alcohol known as ohaguro (“teeth blackening liquid”) to produce a unique, dark finish.
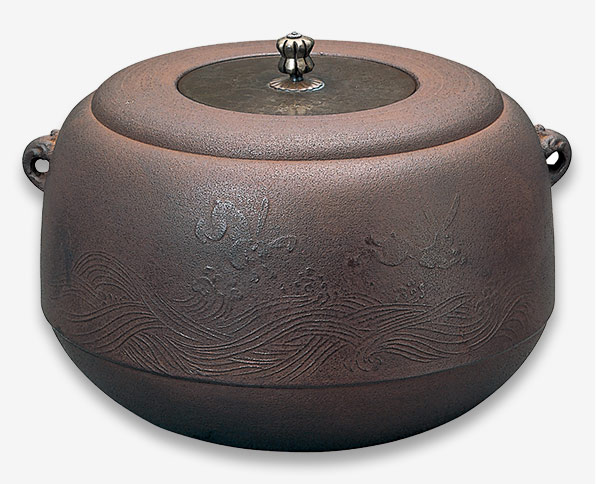
Sectioned mold casting
In sectioned mold casting (komegata) a plaster mold is taken from a clay model. The mold is then covered with clay to produce an outer mold, followed by a slightly smaller inner mold.
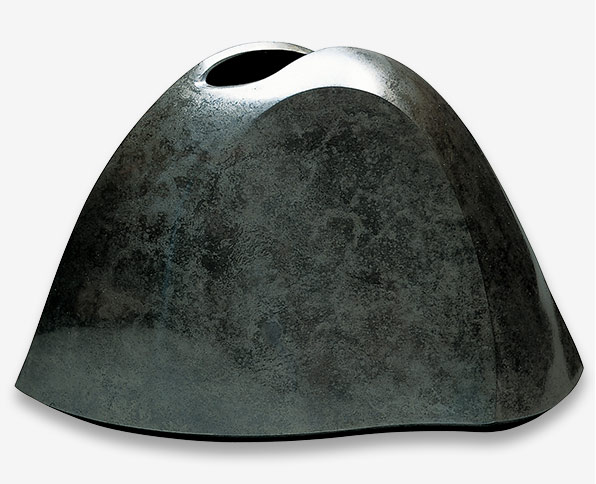
Multiple metal casting
Multiple metal casting (fukiwake) is a technique in which two or more different types of molten metal are cast together in the same mold. The metals are added consecutively and produce works with elegant, flowing patterns.
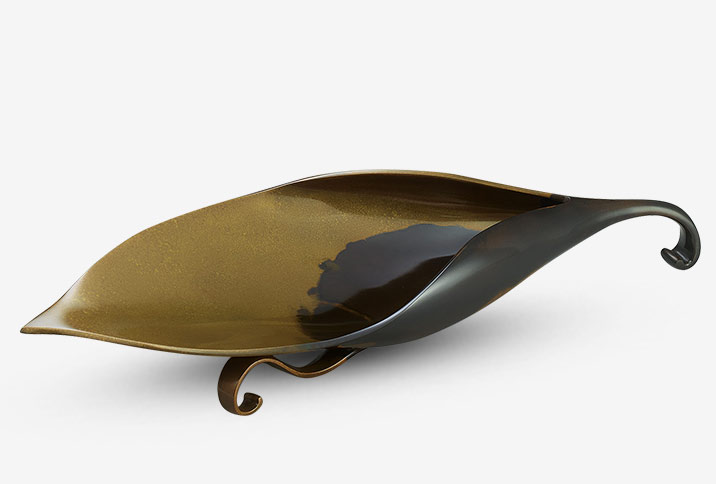
Hammer forming
Forms are shaped with a hammer
Hammer forming
In hammer forming (tankin), a mallet is used to shape a sheet of metal by hammering it into recessions in a wooden stump or block. Next, the metal sheet is worked on the end of specially shaped iron bars known as forming stakes (ategane) to gradually create the final form. It takes tens of thousands of hammer strikes to produce a single finished work.
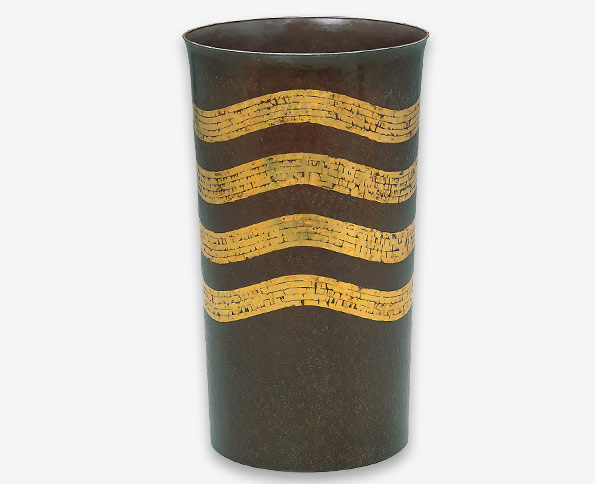
Hard soldering
Hard soldering (hagiawase) is a technique used join together different types of metal sheet. The technique makes it possible to create metalwork with striped or patchwork patterns. Once joined, the artisan may continue to shape the metal with a hammer.
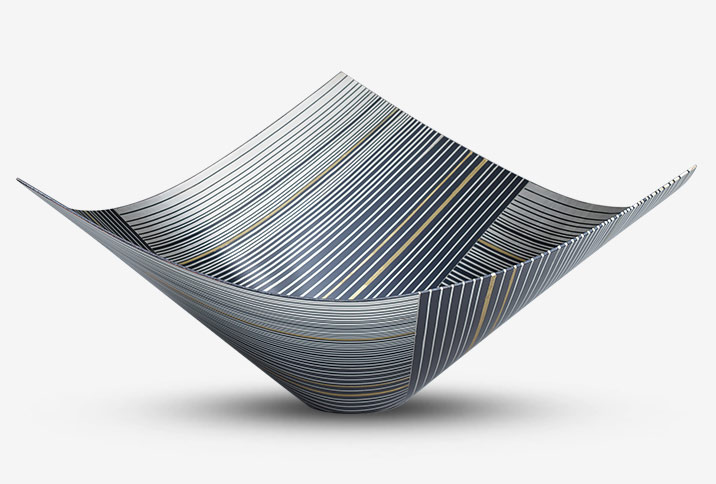
Mokumegane
Mokumegane (“wood-grain metal”) is a decorative metal laminate characterized by polychromatic wood-like grain patterns. The pattern is made by soldering together sheets of different metals to form a layered billet that is then hammer worked and cut to reveal the pattern. The metal may then be further worked to create objects with the unique patterning.
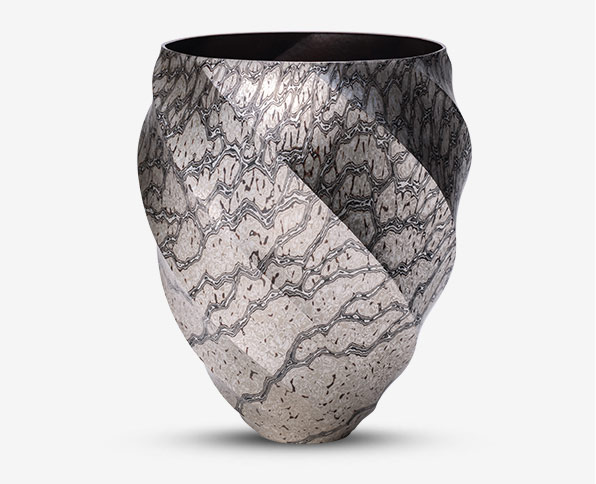
Chisel work
Decorative techniques
Chisel engraving
Chisel engraving (hori) consists of using engraving chisels to embellish the surface of metalwork. Techniques include standard hairline engraving (kebori) performed with a V-shaped chisel, wedge-shaped dot engraving (keribori) performed with a triangular chisel, and metal cutting (hatsuribori) performed with especially sharp flat chisels.
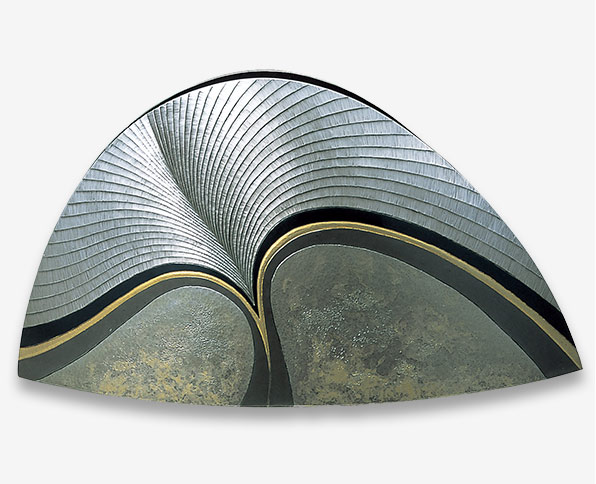
Metal inlay
In metal inlay (zōgan), designs are cut into the surface of a piece and inlaid with a different metal of contrasting color or texture.
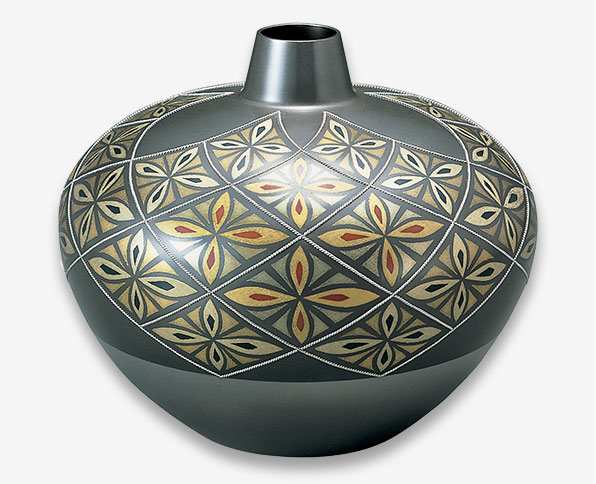
Embossing
Embossing, or metal chasing (uchidashi), is the process of using punches to raise designs on metal by repeatedly hammering the face or back of a piece (the latter technique being known as “repoussage”). Embossed work can take the shape of highly pronounced three-dimensional forms or shallow reliefs like those seen on brooches and ornaments for kimono obi.
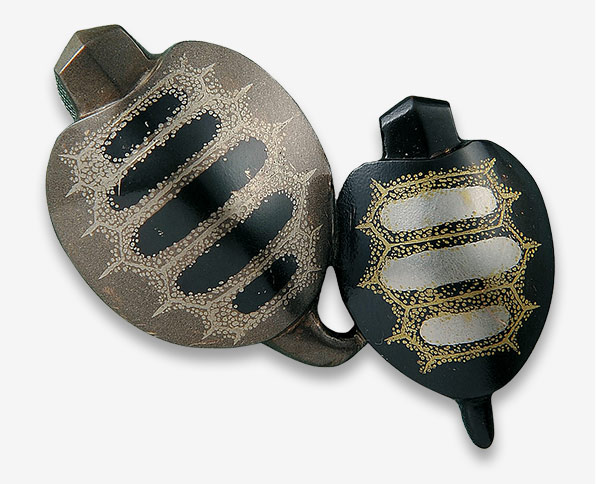
Metal overlay
In metal overlay (nunome zōgan), a chisel is used to create patterns of fine crosshatching over which leaves of gold, silver, or lead may be affixed to create decorative surface details. Literally “cloth-pattern inlay,” nunome zōgan takes its name from the distinctive crosshatching pattern used to affix the metal leaf.
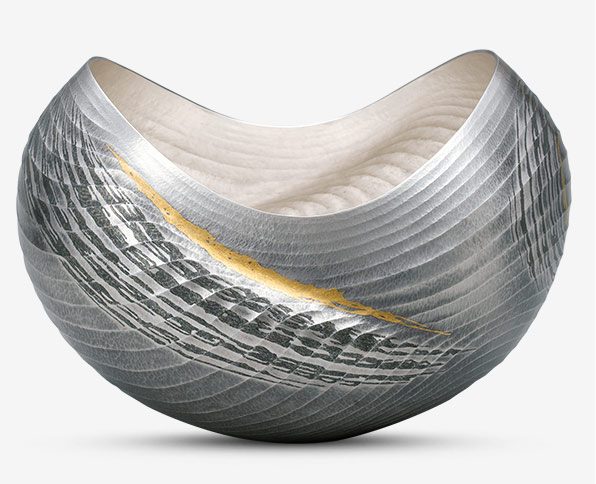
Metalwork Artists
Main Production Areas
Nambu ironware
Nambu ironware is rust-resistant, long-lasting, wellinsulated, and provides a uniform circulation of heat. The exterior of the iron kettles have a bumpy textured pattern called arare meaning hailstone which is often used to help increase the surface area.
Takaoka copperware
The notable features of Takaoka copperware are the skillful hands-on casting techniques of the artisans and the polishing, metal carving and inlaying production techniques. This craft takes on a deeper expression over time and can be enjoyed as it changes throughout the years.
Yamagata cast iron
Yamagata Cast Metal is a metalwork produced around Yamagata City, Yamagata Prefecture. While maintaining the profound presence of ironware, it is thin and has a fine texture. With the evolution of technology, in addition to iron products, copper alloy and aluminum cast metal products are also increasing.
Higo inlays
Higo Inlays is a metalwork produced in Kumamoto City, Kumamoto Prefecture. The craft started as decorations for gun barrels and sword guards, but today the techniques are used in personal accessories and interior decorations.